Passive power supply load tester is unavoidable part of the embedded system design process. It allows to determines the current/power headroom of the designed power rails and their thermal profiles.
Requirements:
- Ability to control current consumption in discreet steps
- Current, voltage and power consumption measurement
- Support up to 32V power rail
- USB interface for system control and monitoring
- Display for system status
Major components:
- STM32G474
- 12x 16W resistors
- 320×240 display
Number of PCB layers: 4
BOM price: 75 USD
Realization time: 4 weeks
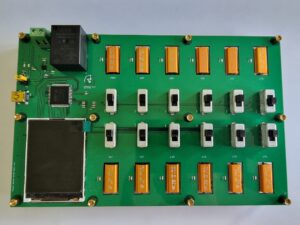
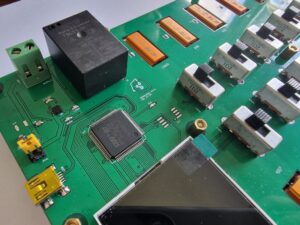
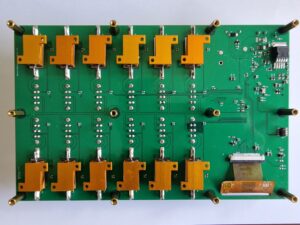